Pemanfaatan limbah piston bekas sebagai filler metal aluminium pada pengelasan oxy-acetylene
Abstract
The abundance of waste piston used so far has not been utilized properly. Users of this piston waste can be used as an oxy-acetylene welder filler. Las oxy-acetylene has been widely used for welding on various types of aluminum product repair, one of which is welding machine block. Machine blocks in their use often suffered damage to the cooling water circulation path and broken crack and broken. Welders and repair shops that repair these damages do not have standardized standards in the use of weld fillers, but they do filler selection based solely on experience including in determining the weld filler. The purpose of this research is to know the effect of piston waste which is used as raw material of weld filler to tensile strength and hardness of welded block result of machine using oxy-acetylene welding. Welding is done by an experienced welder. The welding results are tested for tensile strength and hardness distribution test. The welded joint with the chemical composition of filler which is almost equal to base metal has the highest tensile strength. The tensile strength of the welded joint tension test is in the weld metal region due to defects in the weld metal, especially the porosity defects that are formed during the welding process so that the tensile test loading is concentrated on the defect. While the highest hardness on the weld is in the filler metal with the highest percentage of Si content.
Full Text:
PDFReferences
Abdillah F., 2010, Perlakuan panas paduan Al-Si pada prototipe piston berbasis material piston bekas, Program Studi Magister Teknik Mesin, Universitas Diponegoro Semarang.
Akhtar S.H., 2010, Hydrogen porosity in Al-Si foundry alloys, Department of Materials Science and Engineering, Norwegian University of Science and Technology.
Bangyikhan K., 2005, Effects of oxide film, fe-rich phase, porosity and their interactions on tensile properties of cast Al-Si-Mg alloys, School of Metallurgy and Materials, The University of Birmingham.
Edwards G.A., Sigworth G.K., Cacers C.H., John D.H.St., Barresi J., 1997, Microporosity formation in Al–Si–Cu–Mg casting alloys, AFS Trans.
Liu H.J., Fujii H., Maeda M., Nogi K., 2003, Tensile properties and fracture locations of friction-stir-welded joints of 2017-T351 aluminum alloy, Journal of Materials Processing Technology, 142, 692–696.
Shabestari S.G., Moemeni H., 2004, Effect of copper and solidification conditions on the microstructure and mechanical properties of Al–Si–Mg alloys, Journal of Materials Processing Technology, 153–154.
Sudargo P.H., Triyono, Diharjo K., 2011, Pengaruh filler dan arus listrik terhadap sifat fisik-mekanik sambungan las gmaw logam tak sejenis antara baja karbon dan J4, Pasca Sarjana Jurusan Teknik Mesin, Universitas Sebelas Maret Surakarta.
Suratman R., 2011, Beberapa kasus pada pengelasan, API-IWS, http://www.api-iws.org/beberapa-kasus-pada-pengelasan. html.
Turan E., Kocal T., Ünlungencoglu K., 2011, Welding technologies in shipbuilding industry, The Online Journal of Science and Technology, 1(4).
Wiryosumarto H., Okumura T., 2000, Teknologi pengelasan logam, PT. Pradnya Paramita, Jakarta.
DOI: https://doi.org/10.29303/dtm.v7i2.160
Refbacks
- There are currently no refbacks.
Copyright (c) 2017 Dinamika Teknik Mesin

This work is licensed under a Creative Commons Attribution-NonCommercial 4.0 International License.
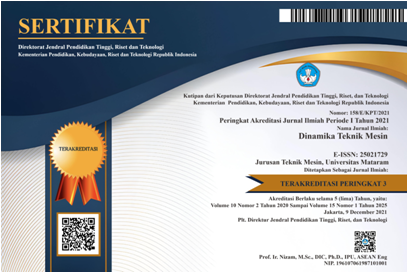