Analysis of carbide tool wear during turning of aisi 4340 with variations in cutting speed
Abstract
Keywords
Full Text:
PDFReferences
Aminy, A., Arsyad, H., Fahri, Hayat, A., Investigation of surface roughness and tool wear in milling of AISI 4340 steel, Journal of Physics: Conference Series, 2739, 012042, 2024.
Devillez, A., Le Coz, G., Dominiak, S., Dudzinski, D, Dry machining of Inconel 718, workpiece surface integrity, Journal of Materials Processing Technology, 211(10), pp. 1590–1598, 2019.
Fahrizal, F., Suprapto, E., P., B., Optimization of machining parameters for minimizing tool wear in turning of low-carbon steel, Jurnal Pendidikan Teknik Mesin Undiksha, 10(1), pp. 10–19, 2022.
Ghani, J. A., Choudhury, I. A., Hassan, H. H., Application of Taguchi method in the optimization of end milling parameters, Journal of Materials Processing Technology, 145(1), pp. 84–92, 2021.
Jena, J., Panda, A., Behera, A., Jena, P., Das, S., Dhupal, D., Modeling and optimization of surface roughness in hard turning of AISI 4340 steel with coated ceramic tool, Proceedings of ICEMIT 2017 (Vol. 2). Springer, 2019.
Junaidi, J., Yulfitra, Y., Study of surface quality in dry turning of AISI 4340 steel using PVD and CVD coated tools, Jurnal Simetri Rekayasa, 3(2), pp. 234–240, 2021.
Lubis, S. Y., Djamil, S., Adianto, A., Santosa, A., VM, E., Variation in cutting speed in the turning process of AISI 4140 steel on tool wear and carbide tool life, Poros, 17(1), p. 26, 2021.
Purnawarman, O., Sambas, A., Rukmana, B., Optimization of turning parameters on AISI 4340 material using Taguchi and grey relational analysis method, Jurnal Teknologi Terapan [Online], 10(1), pp. 10–18, 2024.
Rahmi, M., Rachmatulllah, R., Sukardi, C., The effect of turning process on AISI 4140 steel on mental workload using NASA-TLX method, Jurnal Rekayasa Mesin, 12(2), pp. 361–369, 2021.
Rochim, T., Teori dan teknologi proses pemesinan. Bandung: Penerbit HEDS, 1993.
Saputro, E. D., Martowibowo, S. Y., Tabah, G., Validation of surface roughness and tool wear optimization in turning process using Taguchi method with single data, Jurnal Teknik: Media Pengembangan Ilmu dan Aplikasi Teknik, 23(1), pp. 75–82, 2024.
DOI: https://doi.org/10.29303/dtm.v15i1.943
Refbacks
- There are currently no refbacks.
Copyright (c) 2025 Open access

This work is licensed under a Creative Commons Attribution-NonCommercial 4.0 International License.
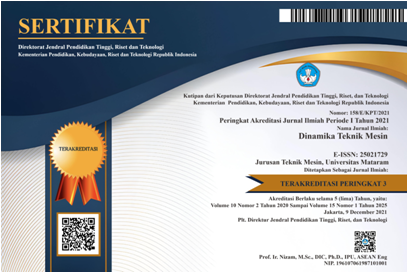